Because some 85% of human
impressions are visual, proper quantity and quality of light are
essential to optimum performance. The mission of lighting
management is to provide the optimum quantity and quality of light
to its users at the lowest operating cost.
Lighting metrics are used to
understand and predict how a lighting system will operate. They
deal with quantity of light (light output and light levels),
quality of light (brightness and color), and fixture efficiency
(electrical efficiency and how much light leaves the
fixture).
QUANTITY OF LIGHT
Luminous Flux (Light Output). This
is the quantity of light that leaves the lamp, measured in lumens
(lm). Lamps are rated in both initial and mean lumens.
Initial lumens indicate how much
light is produced once the lamp has stabilized; for fluorescent and
high-intensity discharge (HID) lamps, this is typically 100
hours.
Mean lumens indicate the average
light output over the lamp's rated life, which reflects the gradual
deterioration of performance due to the rigors of continued
operation; for fluorescent lamps, this is usually determined at 40%
of rated life.
A number of factors affect a lamp's
light output over time, including lamp lumen depreciation, the
lamp's interaction with the ballast, supply voltage variations,
dirt or dust on the lamp, and the ambient temperature in the
fixture.
To avoid confusion, note that
"lumen output" is a term also used to describe a fixture's light
output, not just a lamp's. Even more factors can affect light
output in this case, including the distribution characteristics of
the fixture, fixture surface depreciation, and dirt and dust
buildup.
Illuminance (Light Level). This is
the amount of light measured on the workplane in the lighted space.
The workplane an imaginary horizontal, tilted or vertical line
where the most important tasks in the space are performed. Measured
in footcandles (fc) (or lux in metric), light levels are either
calculated or, in existing spaces, measured with a light meter. A
footcandle is actually one lumen of light density per square foot;
one lux is one lumen per square meter. Like lumens, footcandles can
be produced as either initial or maintained quantities.
Initial footcandles indicates a
light level after new lamps are installed.
Maintained footcandles indicates a
light level after light loss factors are considered over a period
of time. Light loss factors include those affecting light output
(see above) and also room surface reflectances, room
size/proportions, dirt and dust buildup. While light output may
describe either the output of a light source or fixture, maintained
footcandles always takes into account the efficiency of the fixture
in transmitting light to the workplane.
The human eye is a sophisticated
piece of machinery; it is able to adjust to a wide range of light
levels, including about 10,000 footcandles on a sunny day to about
0.01 footcandles under full moonlight. However, optimum ranges of
light levels have been established for various tasks so that those
tasks are performed most efficiently (reading a magazine, for
example, would be difficult under moonlight, while 10,000
footcandles would be excessive).
For more information, see Lighting
Design Basics and Light Loss Factors.
QUALITY OF LIGHT
Luminance (Photometric Brightness).
The light that we actually see, brightness can be measured as the
light leaving a lamp, or the light reflecting from an object's
surface. If not controlled, brightness can produce levels of glare
that either impair or prevent a desired task being performed. Glare
can be described as direct or reflected glare, which can then
result in discomfort or disability.
Direct glare comes straight from
the light source.
Reflected glare shows up on the
task itself, such as a computer screen.
Discomfort glare does not prevent
seeing makes it uncomfortable.
Disability glare prevents vision. A
popular example is holding a glossy magazine at a certain angle; a
veiling reflection results, impairing our reading of the
page.
Color. The color quality of a lamp
is revealed as its color temperature rating and Color Rendering
Index (CRI) rating. For a detailed description of these metrics,
see
Color Metrics.
FIXTURE
EFFICIENCY
There are two ways to look at a
light fixture's (luminaire's) efficiency; one indicates how well
the lighting system transforms electrical input into useful light
output, and the other indicates how well the fixture itself
transmits light from the lamp(s) to the workplane.
Electrical Efficiency. Lighting
systems require electrical input to work. This input is measured in
watts (W), a measure of required electric power. A lighting
system's rated input wattage, therefore, is the amount of power
required for it to work at any given instant of time.
Lamp manufacturers publish nominal
wattage ratings for their lamps; when fluorescent and HID lamps are
operated as a system with a ballast, however, a new rated wattage
will result, published by the ballast manufacturer. Ballast
manufacturers publish up to three input wattage ratings. The ANSI
number is the result of a standardized ANSI test of that given
ballast manufacturer's ballast operating a given compatible lamp
type (often called the "bench test" because the lamps and ballasts
are operated bare on a bench). The next one or two are the
manufacturer's ratings for tests in actual open and/or enclosed
fixtures.
While the manufacturer's ratings
can be considered more realistic (because the testing takes place
closer to actual field conditions), the ANSI number should be used
when comparing different ballasts because it reflects the results
of a common, standardized test procedure.
Therefore, one way to compare the
electrical efficiency of lamp-ballast systems is to determine a
common light output level, then compare the input wattage for
various systems.
A more popular way of achieving a
comparison of the relative efficiencies of lighting systems is to
use efficacy, expressed in lumens per watt (LPW or lm/W). To
determine a system's efficacy, divide its lumen output by its rated
input wattage.
When lighting professionals apply
the results of efficiency to actual system operation (usually to
determine the operating cost savings of a retrofit, they need to
determine the amount of energy the lighting system consumes, not
just its input wattage. To calculate the energy use of a lighting
system, multiply input wattage (W) x time (hours of operation
during a year).
Example for Lighting
System:
Input Wattage
|
100W
|
|
Lumen Output
|
10,000 lm
|
|
Efficacy
|
100 LPW
|
10,000 lm ÷ 100W
|
Hours of Operation
|
3,120 h
|
5 days/week x 12 hours/day x 52
weeks/year
|
Energy Use
|
312,000 Wh
|
100W x 3,120 hrs/year
|
Energy Use
|
312kWh
|
312,000 watt-hours (Wh) ÷
1,000 = 312 kilowatt-hours (kWh)
|
Utility Charge/kWh
|
$0.075
|
|
Energy Cost/Year
|
$23.40
|
312kWh x $0.075/kWh
|
For more information, see
Retrofit
Economics.
Fixture Efficiency. The light
fixture's physical characteristics will affect how much light will
leave the fixture and how much will be directed at the task.
Factors that affect the efficiency of the fixture include its
shape, the reflectance of its materials, how many lamps are inside
the fixture (and how close they are to each other), and whether
shielding material such as a lens or louver is used to soften or
scatter the light.
To compare fixture efficiencies in
a given environment, designers often use a derating factor called
the coefficient of utilization (CU). This value shows the
percentage of lumens produced by the lamps that reach the workplane
after light is lost due to the fixture's efficiency at transmitting
light, the room proportions, and the ability of room surfaces to
reflect light. Determining the most accurate CU value for various
fixtures in a new or renovation space requires use of the Zonal
Cavity Method. For more information about CU values for generic
fixture types, see the latest edition of the Illumination
Engineering Society of North America IESNA Lighting
Handbook.
The National Lighting Collaborative
has developed the Luminaire Efficacy Rating, or LER, part of a
voluntary program being implemented by the lighting industry. A
free publication is available describing the LER.
Light
Guide:
Color Metrics
|
|
Basic Principles
Light, like all forms of radiant
energy, is represented on the electromagnetic spectrum. Traveling
in waves, light is differentiated from other forms of radiant
energy such as heat and X-rays by the frequency and length of its
waveform. A narrow band on the spectrum is visible light, composed
of different colors/wavelengths, from violet at 380 nanometers to
red at 620-760 nanometers. An even balance of these light waves
composes white visible light. To see this principle firsthand, look
at a rainbow, which results from sunlight being refracted by
droplets of moisture in the air, or simply shine a beam of white
light through a glass prism to make a rainbow of colors appear on
the other side.
Visible light cannot be seen,
however. If we turned on a flashlight in a dark room, the beam of
light we are seeing is actually light being reflected from a
multitude of dust particles in the air. Therefore, we see objects
only when light is reflected or emitted from them. And that is how
we see color.
All objects are chemically oriented
to absorb certain wavelengths of light and reflect others. The ones
that are reflected are perceived by the human eye to be the color
of the object. A red object being struck by visible white light
will absorb all wavelengths except red, which is reflected, and so
we see the object as red. A pure white object reflects all
wavelengths and absorbs none. A pure black object absorbs all
wavelengths and reflects none.
This is where a great amount of art
comes into lighting because few lamp types produce pure white
light. Some lamps produce light that is saturated in blue and
green, others red and yellow. A red object struck by light that
contains only blue and green wavelengths would not appear red as if
it were under sunlight. A low-pressure sodium lamp produces light
saturated in yellow, which means that all objects struck by it will
appear yellow, black or a shade of gray. The major lamp
manufacturers all have literature and exhibits that demonstrate the
effect of light on color. The slogan of one: "Color is how you
light it."
Metrics
To understand how a lamp's light
will affect the color of objects in the space, three metrics are
used, including spectral power distribution, color
temperature and color rendering.
Spectral power distribution
shows the visible light spectrum and the wavelength composition for
the light from the lamp (see illustration). The spikes indicate
that the light is stronger in revealing certain colors.
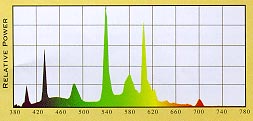
A spectral power distribution curve for a 400K
lamp with a triphosphor (red, blue, green) coating to improve color
rendering. Courtesy of Osram Sylvania
|
Color temperature, expressed
on the Kelvin scale (K), is the color appearance of the lamp itself
and the light it produces.
According to the Illuminating
Engineering Society of North America (IESNA), color temperature is
"the absolute temperature of a blackbody radiator having a
chromaticity equal to that of the light source."
Imagine a block of steel that is
steadily heated until it glows first orange, then yellow and so on
until it becomes blue or bluish-white. At any time during the
heating, we could measure the temperature of the metal in
Kelvins (Celsius + 273) and assign that value to the color
being produced, resulting in a "color temperature." Computer
software performs this function for today's lamps, giving them a
color temperature rating found in the manufacturers'
literature.
For incandescent lamps, the color
temperature is a "true" value; for fluorescent and high-intensity
discharge (HID) lamps, the value is approximate and is therefore
called correlated color temperature. In the industry, both
terms - - color temperature and correlated color temperature - -
are often used interchangeably. The color temperature of lamps
makes them visually "warm," "neutral" or "cool" light
sources.
Lamps with a lower color
temperature (3500K or less) have a warm or
red-yellow/orangish-white appearance. The light is saturated in red
and orange wavelengths, bringing out warmer object colors such as
red and orange more richly.
Lamps with a mid-range color
temperature (3500K to 4000K) have a neutral or white appearance.
The light is more balanced in its color wavelengths.
Lamps with a higher color
temperature (4000K or higher) have a cool or bluish-white
appearance. Summer sunlight has a very cool appearance at about
5500K. The light is saturated in green and blue wavelengths,
bringing out cooler object colors such as green and blue more
richly.

These three photos simulate the effects of color
temperatures on objects. (Left) a warm light source is used,
enhancing reds and oranges while dulling blues and greens; (Middle)
a neutral source is used; (Right) a cool source is used enhancing
blues and greens while dulling reds and oranges. Courtesy of Osram
Sylvania
|
Once a color temperature is
specified, use the spectral power distribution data to aid in
selecting a specific lamp.
Color rendering, expressed
as a rating on the Color Rendering Index (CRI), from 0-100,
describes how a light source makes the color of an object appear to
human eyes and how well subtle variations in color shades are
revealed. The higher the CRI rating, the better its color rendering
ability.
According to the IESNA, color
rendering is the "measure of the degree of color shift objects
undergo when illuminated by the light source as compared with the
color those same objects when illuminated by a reference source of
comparable color temperature."
Imagine two objects, one red, one
blue, that are lighted by a cool light source with a low CRI. The
red object appears muted while the blue object appears a rich blue.
Now take out the lamp and put in a cool light source with a high
CRI. The blue object still appears a rich blue, but the red object
appears more like its true color.
Standard incandescent lamps enjoy a
CRI rating of 100. Fluorescent lamps are in the 52-95 range,
depending on the lamp. Advances in phosphor technology have enabled
fluorescent and HID lamps to advance greatly in color
rendering.
As stated in the IESNA definition,
to compare any two given lamps, they must have the same color
temperature for the comparison to have any meaning.
Specifying Color
When specifying color
characteristics for a lamp, numerous psychological factors must be
considered depending on the lighting goals for the space. Here are
a few general tips.
Warm light sources are generally
preferred for the home, restaurants and retail applications to
create a sense of warmth and comfort, while neutral and cool
sources are generally preferred for offices and similar
applications to create a sense of alertness.
In addition, in retail
applications, color is a critical design decision because buyers
need to be able to choose products of the correct color, both to
enhance the chance of its sale and to reduce the chance of it being
returned once the buyer gets outside and sees it under sunlight. In
this or any other application where the occupant needs to see the
right color, good color quality is essential.
In other applications such as
parking lots, color is not an important factor, so
low-color-rendering lamps can be specified.
|
Light
Guide:
Useful Formulas
|
ELECTRICAL
FORMULAS
Demand for Power (kW) = System
Input Wattage (W) ÷ 1,000
Energy Consumption (kWh) = System
Input Wattage (kW) x Hours of Operation/Year
Hours of Operation/Year = Operating
Hours/Day x Operating Days/Week x Operating Weeks/Year
Lighting System Efficacy (Lumens
per Watt or LPW) = System Lumen Output ÷ Input
Wattage
Unit Power Density (W/sq.ft.) =
Total System Input Wattage (W) ÷ Total Area (Square
Feet)
Watts (W) = Volts (V) x Current in
Amperes (A) x Power Factor (PF)
Voltage (V) = Current in Amperes
(A) x Impedance (Ohms) [Ohm's Law]
ECONOMIC FORMULAS
Simple Payback on an Investment
(Years) = Net Installation Cost ($) ÷ Annual Energy Savings
($)
5-Year Cash Flow ($) = 5 Years -
Payback (Years) x Annual Energy Savings ($)
Simple Return on Investment (%) =
[Annual Energy Savings ($) ÷ Net Installation Cost ($)] x
100
DESIGN FORMULAS
Footcandles &
Lumens
Footcandles (fc) = Total Lumens
(lm) ÷ Area in Square Feet
1 Lux (lx) = 1 Footcandle (fc) x
10.76
Lux = Total Lumens
÷ Area in Square Meters
Calculating Light Level at a
Point
For planes perpendicular to the
direction of candlepower (Inverse Square Law):
Footcandles (fc) = I ÷
D2
I = Candlepower in
candelas (cd)
D = Direct distance between the
lamp and the point where light level is calculated
Many workplanes are not
perpendicular to the direction of light intensity, which is why
calculating light level at a point is useful for such applications.
In these cases, we often must determine light levels on workplanes
that are not horizontal and perpendicular but tilted or even
vertical. For tilted-horizontal or vertical planes:
Horizontal Footcandles
(fch) = (I ÷ D2) x H
Vertical Footcandles
(fcv) = (I ÷ D2) x L
I = Candlepower in
candelas (cd)
D = Direct distance between the
lamp and the point where light level is calculated
H = Distance between the lamp and
the point direct below on the workplane
L = Distance between that point and
the point where light level is being calculated
D = Square Root of (H2 +
L2) or D2 = H2 +
L2
Calculating Average Light Level
Throughout a Space (three formulas)
Average Maintained
Illumination (Footcandles) = (Lamps/Fixture x Lumens/Lamp x No. of
Fixtures x Coefficient of Utilization x Light Loss Factor) ÷
Area in Square Feet
Average Maintained Illumination
(Footcandles) = (Total Lamps x Lumens/Lamp x Coefficient of
Utilization x Light Loss Factor) ÷ Area in Square
Feet
Average Maintained Illumination
(Footcandles) = (Lamps in One Fixture x Lumens/Lamp x Coefficient
of Utilization x Light Loss Factor) ÷ Area in Square
Feet/Fixture
Lumen Method
Required Light Output/Fixture
(Lumens) = (Maintained Illumination in Footcandles x Area in Square
Feet) ÷ (Number of Fixtures x Coefficient of Utilization x
Ballast Factor x Light Loss Factor)
Light Loss Factors (more
on Light Loss)
Light Loss Factor (LLF) = Ballast
Factor x Fixture Ambient Temperature Factor x Supply Voltage
Variation Factor x Lamp Position Factor x Optical Factor x Fixture
Surface Depreciation Factor x Lamp Burnouts Factor x Lamp Lumen
Depreciation Factor x Fixture Dirt Depreciation Factor x Room
Surface Dirt Depreciation Factor
Lamp Burnout Factor = 1 -
Percentage of Lamps Allowed to Fail Without Being
Replaced
Zonal Cavity Method (determining
cavity ratios)
Room Cavity Ratio (for
regular rooms shaped like a square or rectangle) = [5 x Room Cavity
Depth x (Room Length + Room Width)] ÷ (Room Length x Room
Width)
Room Cavity Ratio (for
irregular-shaped rooms) = (2.5 x Room Cavity Depth x Perimeter)
÷ Area in Square Feet
Ceiling Cavity Ratio = [5 x Ceiling
Cavity Depth x (Room Length x Room Width)] ÷ (Room Length x
Room Width)
Floor Cavity Ratio = [5 x Floor
Cavity Depth x (Room Length x Room Width)] ÷ Room Length x
Room Width
Room surface reflectances can be
predicted in a new design or measured in an existing facility. If
existing facility:
Room Surface Reflectance
(%) = Reflected Reading ÷ Incident Reading
Reflected Reading = Measurement
from a light meter holding it about 1.5 feet away from the surface
with the sensor parallel and facing the surface.
Incident Reading = Measurement from
a light meter held flat against the surface and facing out into the
room.
Calculating Number of Lamps And
Fixtures And Spacing
Required No. of Fixtures =
(Lumens/Lamp x No. of Lamps x Coefficient of Utilization x Light
Loss Factor x Area in Square Feet) ÷ (Lumens/Lamp x
Lamps/Fixture x Coefficient of Utilization x Light Loss
Factor)
Required Lamps = Required Lumens
÷ Initial Lumens/Lamp
Maximum Allowable Spacing Between
Fixtures= Fixture Spacing Criteria x Mounting Height
Fixture Spacing Criteria:
See the manufacturer's literature
Mounting height: Distance in feet
between the bottom of the fixture and the workplane
Spacing Between Fixtures = Square
Root of (Area in Square Feet ÷ Required No. of
Fixtures)
Number of Fixtures to be Placed in
Each Row (Nrow) = Room Length ÷
Spacing
Number of Fixtures to be Placed in
Each Column (Ncolumn) = Room Width ÷
Spacing
For the above two
formulas, round results to the nearest whole
integer.
Spacingrow = Room Length ÷
(Number of Fixtures/Row - 1/3)
Spacingcolumn = Room Width ÷
(Number of Fixtures/Column -1/3)
If the resulting number of fixtures
does not equal the originally calculated number, calculate impact
on the designed light level:
% Design Light Level = Actual No.
of Fixtures ÷ Originally Calculated No. of
Fixtures
To calculate fixtures mounted in
continuous rows:
Number of Luminaires in a
Continuous Row = (Room Length ÷ Fixture Length) -
1
Number of Continuous Rows = Total
Number of Fixtures ÷ Fixtures Per Row
MAINTENANCE
Lamp Life
Calendar Lamp Life (Years) = Rated
Lamp Life (Hours) ÷ Annual Hours of Operation
(Hours/Year)
Lamp Burnout
Factor
Lamp Burnout Factor = 1 -
Percentage of Lamps Allowed to Fail Without Being
Replaced
Group Relamping
Cost
Annualized Cost ($) = A x (B +
C)
A = Operating Hours/Year ÷
Operating Hours Between Relampings
B = (Percentage of Lamps Failing
Before Group Relamping x Number of Lamps) x (Lamp Cost + Labor Cost
to Spot Replace 1 Lamp)
C = (Lamp Cost, Group Relamping +
Labor Cost to Group Relamp 1 Lamp) x Number of Lamps
Spot Relamping
Cost
Average Annual Cost ($) =
(Operating Hours/Year ÷ Rated Lamp Life) x (Lamp Cost +
Labor Cost to Replace 1 Lamp) x Total Number of Lamps
Cleaning Cost
Cleaning Cost ($) = Time to Wash 1
Fixture (Hours) x Hourly Labor Rate ($) x Number of Fixtures in
Lighted Space
ENVIRONMENTAL
IMPACT
Average Reduced Air Pollution (lbs.
Carbon Dioxide) = Energy Savings (kWh) x 1.6 lbs.
Average Reduced Air Pollution (g.
Sulphur Dioxide) = Energy Savings (kWh) x 5.3 g.
Average Reduced Air Pollution (g.
Nitrogen Oxides) = Energy Savings (kWh) x 2.8 g.
Pounds = Grams ÷
454
Tons = Pounds ÷
2,000
Light
Guide:
Light Source and Fixture Selection
|
|
The lighting design process in its
most basic form entails identifying a task and then providing a
light source that will provide proper quantity and quality of light
for the task. The fixture protects the light source, connects it to
the power source and distributes its light. In this article, we
will review the basic factors that go into specifying a light
source and a fixture.
Light Source Specification
Checklist
The light source is the actual
light-producing component of the lighting system. It may operate
simply as a lamp (incandescent/halogen) or as a lamp powered by a
ballast (fluorescent and high-intensity discharge
[HID]).
Below are considerations for
specifying three basic lamp types:
Incandescent
Lamps
- Do not require a
ballast
- Warm color appearance with a low
color temperature and excellent color rendering (CRI
100)
- Compact light source
- Simple maintenance due to screw-in
Edison base
- Less efficacious light
source
- Shorter service life than other
light sources in most cases
- Filament is sensitive to
vibrations and jarring
- Bulb can get very hot during
operation
- Must be properly shielded because
incandescent lamps can produce direct glare as a point
source
- Require proper line voltage as
line voltage variations can severely affect light output and
service life
Fluorescent Lamps
- Require a ballast
- Range of color temperatures and
color rendering capabilities
- Low surface brightness compared to
point sources
- Cooler operation
- More efficacious compared to
incandescent
- Ambient temperatures and
convection currents can affect light output and life
- All fixtures installed indoors
must use a Class P ballast that disconnects the ballast in the
event it begins to overheat; high ballast operating temperatures
can shorten ballast life
- Options for starting methods and
lamp current loadings
- Requires compatibility with
ballast
- Low temperatures can affect
starting unless a "cold weather" ballast is specified
HID Lamps
- Require a ballast
- Ambient temperature does not
affect light output, although low ambient temperatures can affect
starting, requiring a special ballast
- Compact light source
- High lumen packages
- Point light source
- Range of color temperatures and
color rendering abilities depending on the lamp type
- Long service life
- Highly efficacious in many
cases
- Line voltage variations, possible
line voltage drops, and circuits sized for high starting current
requirements must be considered
Below is a checklist for
specifying the right lamp for the application:
- Light output
- Input wattage
- Efficacy (lumens per
watt)
- Rated service life
- Size
- Surface brightness
- Color characteristics
- Electrical operating
characteristics
- Requirement of additional
equipment such as ballasts
- Compatibility with the electrical
system
- Suitability for the operating
environment
See also Fluorescent Light Sources,
Incandescent Light Sources, HID Light Sources, Demanding
Environments, Color Metrics, Industrial Light Source and Fixture
Selection, Lighting Metrics
Light Fixture Specification
Checklist
A luminaire, often called a light
fixture, is a complete lighting unit that produces and distributes
light. It contains the light source, a ballast if the lamp is
fluorescent or HID, components designed to diffuse or distribute
the light in a controlled pattern, components to protect and
position the lamp(s), and a connection to the power
source.
The light fixture's basic function
is to produce and distribute light to fulfill the design goals for
the lighted space. Below is a checklist for specifying the right
fixture for the job.
Characteristics of The
Space
First, the specifier must fully
understand the demands of the application and conditions in the
space that will affect the operation of the lighting
system:
- Tasks to be performed in the
space
- Desired light levels based on the
tasks performed in the space
- Room size and
dimensions
- Structural obstructions such as
beams
- Layout of furniture and
obstructions such as partitions
- Room and object surface colors and
reflectances
- Special concerns such as safety
and security
- Hours of operation
- Assessment of normal operating
conditions
- Possibility or known existence of
abnormal operating conditions
- Cleanliness of the area during
operation
- Maintenance schedule
- Availability of
daylight
See also Lighting Audits, Demanding
Environments, Planned Lighting Maintenance, Lighting Design: Basic
Principles
Characteristics of Lighting
Components And The Fixture
Now the most appropriate light
source can be selected, followed by the fixture. The specifier must
understand the factors affecting fixture selection:
- Electrical, physical and operating
characteristics of the light source selected
- Electrical, physical and operating
characteristics of appropriate ballasts
- Electrical, physical and operating
characteristics of controls to be employed
- Fixture efficiency (% lamp light
output transmitted out of the fixture)
- Distribution pattern
- Glare control
- Finish
- Appearance
- Size
- Accessibility of interior
components for maintenance
- Ability to handle abnormal as well
as normal operating conditions
- Aesthetics
See also Light Fixtures:
Classifications, Lighting Metrics, Fixtures: Optical Systems,
Lighting Design: Basic Principles, Industrial Light Source and
Fixture Selection, Controlling Glare
|
Light
Guide:
Optical Systems: Methods of Controlling
Light
|
A luminaire, often called a light
fixture, is a complete lighting unit that produces and distributes
light to fulfill the design goals for the lighted space.
The primary methods of controlling
light from a bare light source via a light fixture are reflection,
transmission and refraction. Other methods include polarization,
interference and absorption. In this article, we will discuss the
first three.
Reflection
Reflection, the most common form of
controlling light, occurs when light rays impact and are then
reflected from a surface. The types of reflection
include:
- Specular
- Diffuse
- Spread
- Selective
Specular reflection is when light
is reflected from a highly polished surface such as smooth polished
metal, producing a consistent angle.
Diffuse reflection is when light is
reflected from a rough surface, producing a variety of angles
depending on how the light impacts each tiny part of the rough
surface. Diffuse reflection is typically used to minimize glare,
hot spots and shadows.
Spread reflection is when light is
reflected into a cone of light rays from surfaces such as
corrugated or etched metal, plastic or glass.
Selective reflection is when a
colored surface is used so that only certain color wavelengths or
reflected as opposed to absorbed or transmitted.
As can be seen, how the reflecting
surface is shaped determines how the beam is reflected. The most
popular shapes for such surfaces include circular, parabolic,
ellipsoidal and combination.
Transmission
Transmission occurs when light rays
are passed through a material. The types of transmission
include:
- Direct
- Diffuse
- Spread
- Selective
Direct transmission is when light
rays go through the material with no change to their direction or
color. Example: Clear plate glass.
Diffuse transmission is when light
rays are widely spread, useful when we want to obscure the light
source and produce a uniform appearance of light on the
transmitting surface. Example: Inside-frosted glass.
Spread transmission is when the
maximum intensity of light rays passed through with little change
in direction, producing a glow on the transmitting surface and a
sense of sparkle.
Selective transmission is when
selected color wavelengths are allowed to pass through the
material. Example: Colored glass.
Refraction
Refraction, used in prismatic
lenses in fluorescent fixtures, floodlighting and streetlighting,
occurs when light rays pass through one material and into another
at a different intensity.
|
|
Light
Guide:
Lighting Design: Basic Strategies
|
|
Light plays an essential role in
our ability to perceive the world around us; the lighting system
plays a critical role in how we perceive a space and can even
influence how we act in that space. Lighting can affect
performance, mood, morale, safety, security and
decisions.
The first step in producing the
right lighting design is to ask what the space is used for. The
lighting designer can then determine quantity of light, color
quality, brightness and direction.
It is beyond the scope of this
article to go step by step through the process of producing a
lighting design. Instead, we will review the several ways that
lighting professionals look at lighting design, from the simple to
the sophisticated.
Simple. One way is to ensure
that the lighting system 1) provides ambient illumination
for orientation and general tasks in the space, 2) task
illumination for local, more demanding tasks, and 3) accent
illumination to highlight special objects of interest or to
guide occupants. An example of this scheme is an open office plan
with workstations; we might provide indirect fixtures to provide
ambient illumination, task lighting at the workstations for work,
and accent lighting to highlight pieces of corporate art on the
walls.
Standard. A typical general
approach to lighting design is, after determining how the space is
used, to provide general, localized general, localized and task
illumination to meet these needs. General lighting provides a
generally uniform light level on the workplane throughout the
lighted space. Localized general lighting is similar but is
tailored more to the location of tasks in the lighted space.
Localized lighting, also called supplemental lighting, is used to
provide light to a specific area. Task lighting delivers light
tailored for a specific task.
Sophisticated. A final way
of looking at lighting design is more sophisticated, focused not
only on simply providing quantity of footcandles for tasks with
accent illumination for highlighting, but also on the art of using
light to produce a desired effect.
To explain this last approach,
which deals with how the direction of light is controlled, let us
start with an object.
Key Light. When we shine a
light on an object from a single point source of light it is called
key light; it highlights contours on the object and creates
shadows; the exact effect depends on the angle of the beam of
light. Most of the time we want to light the object to we can see
its front. In these cases, the light source may be best place in
front of and to the side of the object at an angle of
45°.
|

|
|
|
Fill Light. While this scene
effects drama, for our purposes we will assume we need fill light.
It can either be directional or diffused. In our example we could
shine a directional light on the object from the opposite direction
of the key light, softening or eliminating shadows depending on the
strength of the fill light relative to the strength of the key
light. We could also place fill light sources behind the object to
light the entire room evenly. In the Figure below, we see the
keylight supplemented by a single fill light.
|
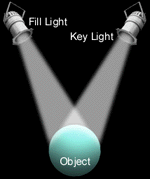
|
|
|
Silhouetting. Suppose we
wanted to emphasize the shape of the object as a silhouette. In
this event, we would soften or even eliminate the key light and
directional fill light, and instead provide only fill light, either
intense or diffused, depending on the clarity of the silhouette and
the drama we want to produce.
|
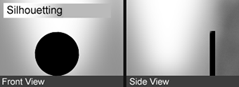
|
|
|
Uplighting. Suppose we
wanted to uplight the object. The effect of uplighting is either
very desirable or very undesirable because it is unusual. Effects
range from intimate to eerie. A lot of landscape lighting includes
uplighting to accentuate bushes and trees.
|
|
|
|
Sparkle And Glitter Effects.
To add an atmosphere of elegance, we could add little lighting
points of interest in the form of sparkle or glitter. This effect
can be produced by either producing sharp reflections on specular
surfaces in the room (sparkle), such as silverware in a restaurant,
or by making the light source itself a source of interest (glitter)
such as with a chandelier. Beware of glare in such
cases.
|
|
|
|
Grazing And Washing
Surfaces. On walls or on the surface of an object, we can
change the way light impacts them so that we can produce different
effects. Suppose we have a brick wall with a rough texture that we
want to emphasize. We could graze the surface with light, meaning
the light would strike the surface at a sharp angle. In this case,
the light source would be mounted close to the wall. Now suppose
the wall is smoother, and we want to emphasize that smoothness. We
could wash the surface with light, meaning the light would strike
the surface at a wider angle.
|
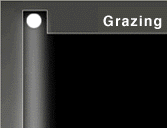
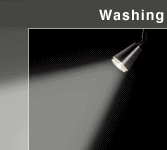
|
|
|
The selection of strategy or
combination of strategies again will depend on how the space is
used. In a retail environment, it might be desirable to provide
strong keylighting to accentuate and dramatize key merchandise,
while in an office such strong concentrations of accentlighting and
shadowing might prove visually fatiguing. Uplighting may work well
in an intimate restaurant or to highlight bottles of alcohol in a
bar, but may make people look sinister in the home or office.
Sparkle and glitter may work well in a restaurant, but might prove
distracting in many industrial work areas.
|
Light
Guide:
Light Loss Factors
|
|
When a light fixture is activated,
it produces light which must leave the lamp, then the fixture, then
reach the workplane where it is needed. Along the way, a number of
operating and environmental conditions interfere with the
transmission of light, resulting in wasted lumens. The lighting
designer must provide a system that will take into account these
conditions so that despite them the lighting system will provide
proper quantity of light over time.
These conditions are captured as
metrics called the light loss factors. Metrics are used to perform
how something behaves. Light loss factors are captured as
percentages or decimals (example: 0.95), which are then multiplied
to result in a final Light Loss Factor in lighting calculations.
There are two types of light loss factors, non-recoverable and
recoverable.
Non-Recoverable Light Loss
Factors
Some light loss factors are called
"non-recoverable" because preventative maintenance generally does
not affect the extent of the light loss. These include ballast
factor, ambient fixture temperature, supply voltage variation,
optical factor and fixture surface depreciation.
Ballast Factor
Lamps and ballasts experience
losses when operating together as a system. The percentage of a
lamp's initial rated lumens produced by a given ballast is called
the Ballast Factor.
Ambient Fixture
Temperature
This factor deals with fluorescent
systems. Deviations above or below the ideal fixture operating
temperature can affect the amount of light leaving the
lamp.
Supply Voltage
Variation
High or low voltages fed to lamps
(incandescent) or ballasts (fluorescent and HID) from the
building's power distribution can result in an increase or decrease
of a lamp's lumen output. Electronic ballasts are not as sensitive
to small variations in supply voltage as magnetic ballasts. Some
models provide constant light output at +10% variation. The IESNA
Lighting Handbook contains supply voltage variation data for
various generic lamps; another source of information is the
manufacturer's literature.
IOptical Factor
The amount of space lamps take up
serves as an obstruction to light leaving the fixture that is
reflected internally. Since lamps absorb mass, they absorb some of
this light output. The result is what is called the Optical Factor.
T12 lamps have an Optical Factor of 1. Removing lamps, or
installing thinner-diameter T10 or T8 lamps, can result in a higher
Optical Factor.
Fixture Surface
Depreciation
As a fixture ages, its surfaces
begin deteriorate. Blemishes absorb light instead of reflecting it;
shielding materials may begin to discolor due to constant exposure
to heat. This light loss factor is difficult to predict.
Recoverable Light Loss
Factors
Some light loss factors are called
"recoverable" because preventative maintenance can reduce the
extent of the light loss. These include lamp burnouts, lamp lumen
depreciation (LLD), fixture (luminaire) dirt depreciation (LLD) and
room surface dirt depreciation (RSDD).
Lamp Burnouts
When a lamp expires, it becomes a
"burnout." Lighting designers usually assume that the burnout will
be replaced immediately. However, if it is known that a percentage
of the lamps are burnouts at any given time, then a light loss
factor must be reckoned with. For example, if 5% of the lamps are
burnouts at any given time, then this light loss factor would be
0.95. Remember that 100% rated life is defined when 50% of the
lamps in a large sample of lamps have failed.
Lamp Lumen
Depreciation
As a lamp ages and nears end of
life, it produces less and less light on a predictable curve, the
extent of which depending on the type of lamp. If group relamping
is employed as a planned maintenance strategy, then take the LLD
factor for the point in life at which the lamps are replaced en
masse. Otherwise, use an average, which is at 40% of life. See the
Table below for typical LLD values for typical lamps.
Table. Typical LLD factors for
several lamp types. Note that additional phosphor coatings to
improve CRI in fluorescent lamps improves lumen
maintenance.
F32T8, 85 CRI
|
0.91
|
F32 T8, 85 CRI
|
0.93
|
F96T12/CW "Slimline"
|
0.88
|
F96T12 "Slimline," 85
CRI
|
0.94
|
F96T12HO/CW
|
0.83
|
F96T12/HO, 85 CRI
|
0.90
|
Compact fluorescent
|
0.85
|
Mercury vapor
|
0.79
|
Metal halide
|
0.83
|
High pressure sodium
|
0.91
|
Fixture (Luminaire) Dirt
Depreciation
Dirt and dust present in all
ambient environments are ultimately attracted to and trapped in
electrical equipment. The extent of dust collecting on the lamps
depends on the environment, what type of fixture is in use, whether
it is ventilated or not, and the type of work performed in the
area. The extent of LDD depends on these conditions and also how
often the fixtures will be cleaned. To determine this factor, first
identify the fixture type's maintenance category (I through VI) in
ascending order of imperviousness to dirt and dust intrusion (see
the IESNA Lighting Handbook for more information).
An industrial strip fixture with no
top or bottom enclosure is an example of a Maintenance Category I
fixture. A direct-indirect fixture is a Category II; an industrial
strip fixture with an apertured top and bottom is a Category III.
Deep-celled parabolic fluorescent fixtures are Category IV
fixtures. A lensed fluorescent troffer is a Maintenance Category V
fixture. A pure indirect fixture is a Category VI. See the IESNA
Lighting Handbook for evaluating dirt conditions.
Adding It All
Up
Once all light loss factors are
determined, multiply one against the next (A x B x C …)
until a final Light Loss Factor (LLF) results that can be used in
lighting design calculations.
|
Light
Guide:
Controlling Glare
|
|
Luminance (Photometric
Brightness)
The light that we actually see,
brightness can be measured as the light leaving a lamp, or the
light reflecting from an object's surface. It is measured in
footlamberts (English) or candelas/square meter
(metric).
Brightness can be used for a
variety of purposes, from producing a sense of drama to creating
sparkle and glitter elements in a space. The brighter a task is,
the easier it is to see and the lower the amount of light that is
required. Too little brightness decreases contrast and calls for a
higher light level. But if not properly controlled, high brightness
can produce levels of glare that either impair or prevent a desired
task being performed. Glare can be described as direct or reflected
glare, which can then result in discomfort or
disability.
Direct glare comes straight from
the light source. Reflected glare shows up on the task itself, such
as a computer screen. Discomfort glare does not prevent seeing
makes it uncomfortable. Disability glare prevents vision--a popular
example is holding a glossy magazine at a certain angle; a veiling
reflection results, impairing our reading of the page.
Strategies for Reducing Unwanted
Glare
Strategies commonly employed to
reduce unwanted levels of glare include:
- Indirect lighting that throws more
light upward than downward, diffusing the light and reducing glare
on computer screens
- Parabolic louvers, special lenses
or other diffusing media on fixtures that diffuse the fixture's
light output
- In an office, it may be possible
to de-emphasize the ambient lighting system with reduced light
output and diffusing media, while providing adjustable task
fixtures at workstations
- Relocating the light
source
- Relocating the task or changing
its orientation until the glare is removed
- Changing the surface reflectance
of the task
- Use blinds or shades on windows to
control the amount or transmittance angle of sunlight entering the
space
Visual Comfort
Probability
Visual comfort probability (VCP) is
a rating on a scale of 0-100 given to indoor fixtures (in a uniform
system with identical fixtures) to indicate how well accepted they
are likely to be by the area's occupants. A VCP rating of 75, for
example, indicates that 75% of the occupants in the poorest
location would not be bothered by direct glare. Generally, office
environments require that fixtures have a VCP rating of 70 or more,
although this figure has been revised by some in recent years to 80
or more for environments where visual-task computers are used. The
VCP rating for a given fixture can be found in its photometric test
report. Generally, again, the higher the VCP rating, the lower the
fixture's efficiency at transmitting light to the task.
Shielding Media Characteristics for
Fluorescent 2x4 Recessed Troffer Fixtures:
Shielding Medium
|
Fixture
Efficiency
|
VCP Rating
|
|
|
|
Clear Prismatic Lens
|
60-75%
|
50-70
|
Low-Glare Clear Lens
|
60-75%
|
75-85
|
Deep-Cell Parabolic
Louver
|
50-70%
|
75-95
|
Translucent Diffuser
|
40-60%
|
40-50
|
Small-Cell Parabolic
Louver
|
35-45%
|
99
|
Brightness Ratios
Brightness ratios in a space can
affect how it is perceived. While high ratios of bright to dark in
the space can produce contrast or a sense of drama, it can also be
visually fatiguing during transient adaptation, which describes the
eye adapting to changes in brightness. This can reduce productivity
and can even be hazardous. The right approach is determined by the
application; the IESNA has recommended brightness ratios for a wide
range of environments.
Uniformity
Uniform light and brightness levels
across a space can be desirable but may also be boring; in such
cases, sparkle elements, color and/or other methods can be employed
to create visual interest without causing fatigue.
|
Light
Guide:
Lighting Audits
|
|
The first step to a successful
lighting upgrade is the lighting survey or audit. In this stage,
which is essential to proper planning, the lighting manager gathers
and organizes information about the existing lighting system and
how it is used.
Various software can serve as a
valuable aid in collecting data. One such free resource is
the ProjectKalc program from the U.S. Environmental Protection Agency's Green
Lights Program.
Collect Financial
Information
To conduct a full financial
analysis that will be needed to justify an investment in upgrading
the existing lighting system, gather data about the local utility
rate structure and average charges for energy (kWh) and demand
(kW).
Determine the availability of
rebates from the local utility that may subsidize purchases of
energy-efficient lighting equipment; also determine sources of
financing and create assumptions for tax rates and inflation rates
for materials and labor.
Collect General
Information
Collect floorplans or reflected
ceiling plans for the facility that show fixture locations and room
dimensions (length in feet, width in feet, ceiling heights in feet
and areas in square feet). Be sensitive that renovation work may
have been performed over the years that has changed the original
floorplans and/or reflected ceiling plans. If not available, create
using graph paper.
Label each area (rooms, hallways,
etc.) with a letter for future identification with sets of data
that will be collected. Also label each area with a generic
description (private office #2, lavatory #1, etc.). It may be
desirable to put a sticker on each door hinge during the
room-by-room survey that bears its identity that corresponds with
the floorplan.
Also, gather as much information as
possible about the building and its history; try to determine what
future plans there are if any for the building.
Collect Occupant
Information
A good way to learn about how
occupants feel about their lighting system is with a survey, which
can asks questions such as, "Do you have trouble with light
reflecting off your computer screen?" An additional benefit of
doing this is that it may help create "buy in" among building
occupants for the new lighting system.
Should this path be taken, however,
how caution in evaluating the answers; the occupants know little
about lighting - - in fact, they rarely notice it unless something
goes wrong. For example, an occupant saying there is too much light
in an area probably is saying that it is too bright, which is an
issue of glare, not quantity of footcandles.
Collect Lighting
Information
For each area, identify:
- Hours of operation
- Type and size of
fixtures
- Number of fixtures (hand-held
mechanical counters can help)
- Number of lamps per
fixture
- Number of lamps per
ballast
- Type of lamps
- Type of ballasts
- Specular reflectors if already
installed
- Fixture condition
- Whether fixtures are air-handlers,
part of the air distribution system
- Availability of
daylight
- Tasks that are performed in the
space (with light level targets)
- Use of partitions
- Unique fixture types or physical
features
- Area dimensions
- Height of the tasks
- Fixture mounting
height
- Room surface reflectances and
colors of major objects and room surfaces
Also determine lighting waste
disposal regulations and costs.
Standardized forms can be created
to help capture and organize information by area.
It may be desirable to plot
existing light levels with a light meter, although this may result
in misleading data because the condition of the fixture and point
of life for the lamps may not be consistent from fixture to
fixture. For this reason, it may be desirable to simply calculate
existing light levels.
If the building is large,
information can be extrapolated based on known data. For example,
if the general lighting scheme is based on 2x4 fluorescent
fixtures, and the spacing and room dimensions are known, an
approximate number of fixtures can be extrapolated. Another method
is to gather data for prototypical spaces, and then make
assumptions for how other prototypical spaces are lighted (this
method works best in large, homogenous spaces). However, when it
comes to accuracy, of course, there is no substitute for a complete
walkthrough.
It may be desirable to contact a
lighting consultant to help conduct the walkthrough and
survey.
|
Light
Guide:
Lighting Upgrade Strategies
|
|
Upgrading a lighting system can
reduce energy consumption in two ways. Since Energy = Power x Time,
we can either reduce the lighting system's input wattage (W or kWh)
or reduce its hours of operation. As the kW and the kWh are the
basic products for which an electric utility charges, significant
operating cost savings can result that can pay for the investment
and then reduce a desirable return on that investment (see
Retrofit Economics
).
It is beyond the scope of this
article to discuss in detail every possible retrofit strategy.
Readers are encouraged to see Lighting Upgrades by Damon Wood (The
Fairmont Press, Inc.). For lighting retrofit fundamentals and
retrofit management, the reader may be interested in seeing The
Lighting Management Handbook (The Fairmont Press, Inc.) by the
author. In this article, we will review general approaches to
retrofitting.
Common Upgrade
Strategies:
Upgrade with reduction in light
levels
In some applications, ambient light
levels can be reduced, particularly in spaces where ambient light
is needed only for the task of orientation, in spaces where planned
lighting maintenance is resulting in a light level higher than
originally planned for, and in spaces where IES light level
recommendations have been revised (that is, reduced).
Approaches include dimming,
lamp/ballast removal, specular reflectors, reduced-output
(lower-wattage lamps) and current limiters.
Increase light
levels
This entails increasing light
levels via planned lighting maintenance, specular reflectors,
higher room surface reflectances or higher-output lamps and other
approaches; after light levels are increased, we are then afforded
the options to then reduce light level and save energy as shown
under "upgrade with reduction in light levels."
Maintain light
levels
In these spaces, we need to
maintain current light levels but can do so by retrofitting with
lighting equipment, such as more-efficient lamps and ballasts, to
provide comparable light output at a reduced wattage.
Focus light
levels
In some applications, the overhead
ambient lighting system is doing most of the work in the space,
providing illumination for both ambient and task lighting. In many
of these applications, by providing portable, adjustable task
fixtures at the task locations, we can upgrade to reduce light
levels in the ambient system, since its primary function will be
retasked for orientation only. An example of this approach is an
indirect lighting scheme for ambient illumination, with task
fixtures.
Reduce hours of
use
Controls such as energy management
systems, occupancy sensors and daylight-dimming ballasts can be
installed to control the hours the lighting system is used,
eliminating waste and reducing energy usage.
Before Beginning
Here are some useful guidelines to
remember when attempting a lighting upgrade:
- The lighting system must serve the
design goals of the space; no upgrade should compromise the
system's performance in meeting these goals. The upgrade should
begin with the question, "What is the spaced used for and how does
the lighting support that?"
- There is no magic to new
energy-efficient lighting systems; since all lighting equipment
operates according to the laws of physics, there are always
tradeoffs
- All lighting components must be
compatible to operate properly
- All OSHA safety requirements
should be met when any work is done on the lighting
system
- Ensure that all retrofits are
permanent and understood by the maintenance personnel in a written
and communicated lighting policy, so that old components are not
reintroduced back into the lighting system later (such as when a
screw-in compact fluorescent lamp fails and is then replaced with
an incandescent lamp)
- Planned lighting maintenance can
be an effective means of getting the best results from the lighting
system and can help create energy management
opportunities
- Be sure to include provisions for
legal compliance in disposing of any lighting waste (see Lighting
Waste Disposal)
Typical Fluorescent Fixture
Upgrades
- T8 Lamp/Ballast System
- Specular
Reflectors/Delamping
- Current Limiters
- Daylight-dimming
Systems
- T5 Twin-Tube Lamp/Ballast
System
- T10 Lamps
- 32W Heater Cut-out and 34W
Energy-Saving T12 Lamps
- 25W T12 Lamps/T8
Ballasts
- Premium Magnetic, Cathode Cut-out
(Hybrid), Electronic Ballasts (Full Output, Dimmable, Light-Level
Switching and Low-Wattage)
- Lens/Louver Upgrades
- Indirect Lighting w/Task
Lighting
- Task Lighting w/Reduced Ambient
Lighting
- New Fixtures
Compact Lighting
Upgrades
- Compact Fluorescent
Lamps
- Halogen Lamps
- Krypton Incandescent
Lamps
- Electrodeless Downlight
Lamps
- Compact HID Lamps
- New Fixtures
High-Intensity Discharge (HID)
Lighting Upgrades
- Energy-Saving Metal Halide and
High Pressure Sodium (HPS) Lamps
- Switching to Metal Halide or HPS
Systems
- HID Fixture Reflectors
- High-Bay Compact Fluorescent
Lamps
- Dimming Ballasts
- New Fixtures
Typical Exit Sign
Upgrades
- Compact Fluorescent
Lamps
- Low-Wattage Incandescent
Lamps
- LEDs
- Electroluminescent
Panels
- New Exit Signs
Typical Control
Upgrades
- Lighting Management
Systems
- Dimmable Fluorescent And HID
Ballasts
- Daylight- and Lumen
Maintenance-Dimming Systems
- Electronic Timeclocks
- Occupancy Sensors (many options
available)
- Manual, Step-Level And Panel-Level
Dimming Systems
- Current Limiters
- Capacitive-Switching HID
Systems
|
Light
Guide:
Lighting & HVAC Interactions
|
|
Lighting systems convert only a
minority fraction of their electrical input into useful light
output. Much of the rest is released directly as heat into the
space. Therefore, any upgrade of the lighting system that reduces
input wattage reduces the amount of heat that must be removed by
the air cooling system. This results in air cooling energy savings
during the operation of the building. In new construction, an
energy-efficient lighting design can result in significant savings
in the installed cost of cooling systems.
A rule of thumb in the industry is
that 1 kWh of air conditioning energy is saved for every 3 kWh of
lighting energy. This, however, is often not accurate because it
does not account for different climates. A retrofit in a building
in Alaska, obviously, will not yield the same air conditioning
energy savings benefit as in a building in Florida - in fact, in
Alaska this heat is quite useful, and the retrofit could result in
a much higher heating bill!
In the northern regions, the cost
of additional heating can cancel out the air cooling energy
savings, but in many areas of the United States the air cooling
savings, which will be 0-30% of the lighting energy savings, will
exceed this additional heating cost.
How to Calculate Air Cooling
Energy Savings
Robert Rundquist, PE is the
president of R.A. Rundquist Associates of Northampton, MA and a
professional engineer with nearly three decades' experience in
heating, ventilation and air conditioning (HVAC) system design,
energy analysis and energy calculation research. He offers a
formula to assess a more accurate figure for air cooling energy
savings that was derived from both independent research and
research conducted for the American Society of Heating,
Refrigeration and Air Conditioning Engineers (ASHRAE). It has been
validated by DOE-2 computer runs and other methods.
1. Lighting energy consumption must
be reduced by a specific amount that stays constant throughout the
year. This is most predictable in a retrofit, but can also work for
some controls and other applications where hours of operation are
reduced.
2. Determine the fraction of the
year of the cooling season. (Download The Advanced Lighting Guidelines to get typical cooling seasons in the US)
3. Determine the fraction of the
daily load met by mechanical cooling. Basically, this question
asks, how much of the lighting system's heat must be removed by the
cooling system? Usually this is about 90%, with 10%
dissipated.
4. Determine the air cooling
system's coefficient of performance. Tests on cooling systems have
shown that for every watt (W or kW) put into the system, 2.7 watts
(W or kW) of cool air is produced. The actual figure can vary,
however, due to a range of factors; the 2.7 figure can be used
although it is best to use the actual system's coefficient of
performance.
5. Calculate using the formula
below:
Fraction of Lighting Savings as Air
Cooling Savings =
Fraction of the Year of the Cooling
Season
x Lighting Load Met by Mechanical
Cooling
÷ System's Coefficient of
Performance
6. Example: Suppose we retrofit a
system in Raleigh, North Carolina, which has a cooling season of 30
weeks, and remove 20,000kWh from the lighting load.
Fraction of Lighting Savings as Air
Cooling Savings =
30 ÷ 52 = 0.5769 or
0.58
x 0.9
÷ 2.7
= 0.19
That means that for every 1 kWh of
lighting saved, we save 0.19 kWh of air cooling energy. In our
example, this means that we have removed 3,800kWh (20,000kWh x
0.19) of air cooling load. If the local utility charges an average
commercial rate of $0.065 per kWh, then we have reduced energy
costs by $1,300 per year for lighting and an additional $247 per
year for air cooling.
|
Light
Guide:
Lighting Waste Disposal
|
|
Both lighting upgrades and routine
maintenance entail the removal of lamps and ballasts from the
system. These lamps and ballasts must be disposed of according to
state and Federal regulations; if they conflict, then the stricter
regulations must be obeyed. Mercury-containing fluorescent and
high-intensity discharge (HID) lamps and PCB-containing ballasts
are two types of potentially hazardous waste.
Lamps
All fluorescent and HID lamps have
mercury content. The U.S. Environmental Protection Agency (EPA)
regulates mercury disposal under the Resource Conservation and
Recovery Act (RCRA). Because the cost of testing the lamps may be
prohibitive, it is generally wise to consider all lamps being
disposed of as hazardous waste. As hazardous waste, lamps must
either be recycled or disposed of in hazardous waste landfills as
opposed to municipal solid waste landfills. They cannot be
incinerated.
Small generators are exempt from
RCRA regulations. Small generators are companies that generate less
than 100 kilograms of hazardous waste per month; in terms of lamps
only, this is about 300-350 4 ft. T12 lamps or 400-450 4 ft. T8
lamps per month.
The cost of recycling a 4 ft.
fluorescent lamp can be about $0.50-0.75/lamp vs. about $0.25-$0.50
for landfill disposal (as of 1995, source: EPA Green Lights);
usually, recycling does not make the initial cost of a lighting
upgrade unprofitable. When fluorescent lamps are recycled, the
waste is crushed, then separated into phosphor powder, recovered
mercury, metal and glass that are eventually put to
reuse.
In recent years, the major lamp
manufacturers have introduced a number of low-mercury fluorescent
and HID lamps (example: Philips' Alto fluorescent lamp) that are
designed to pass EPA tests, allowing them to be disposed of in
municipal solid waste landfills. Check with the state hazardous
waste agency or agencies having jurisdiction to see if the lamps
can be disposed of as solid waste.
In addition, both the U.S. EPA and
the states have been relaxing their regulations regarding the
disposal of fluorescent and HID lamps. Again, check with the
applicable state hazardous waste agency or agencies to determine
the specific requirements for handling, storage, transportation and
disposal of mercury-containing lamps.
Also, for more information, contact
the EPA's Hazardous Waste Hotline at (800) 424-9346.
Ballasts
Ballasts manufactured and
distributed in the United States prior to 1979 contain
polychlorinated biphenyls (PCBs), which is a hazardous material.
Since many magnetic ballasts can enjoy a service life of 25 years
or longer, many of these ballasts are still in existence. If a
ballast label is marked "NO PCBs," then it is not a PCB ballast; if
there is no such marking, then the ballast is assumed to contain
PCB fluid. Handling and disposal instructions for ballasts with
PCBs can be found on this EPA web page: www.epa.gov/pcb/guidance.html
See also:
U.S. Energy Legislation
Light
Guide:
United States Energy Legislation
|
|
In 1988 and 1992, two significant
laws were passed that banned the manufacture and distribution of
magnetic ballasts and certain fluorescent lamps that had for many
years served as a workhorse for commercial lighting
applications.
The laws were passed because
technology made new energy-efficient choices readily available and
because a reduction in national energy consumption was perceived as
in the public interest, both for the conservation of fossil fuels
and to reduce air pollution.
Federal Ballast Energy
Law
The Federal Ballast Energy Law
(Public Law 100-357) was enacted in 1988 as part of the National
Appliance Energy Conservation Amendments (NAECA '88).
The law set minimum ballast
efficacy standards for four major fluorescent lamp types that
represented some 85% of all installed fluorescent
ballasts.
As of 1991, ballasts submitted for
testing by the U.S. Department of Energy and complying with NAECA
'88 provisions carry an 'E' symbol on their labels. Ballasts exempt
from NAECA included dimming ballasts and ballasts used in areas
where ambient temperatures reach 0°F or lower.
The new "standard" magnetic ballast
is what is called a premium magnetic ballast, which increases
efficiency to meet NAECA requirements. Other options include
cathode cut-out ("hybrid") ballasts and electronic
ballasts.
National Energy Policy
Act
In 1992, President Bush signed the
National Energy Policy Act, comprehensive energy legislation that
initiated deregulation of the electric utility industry, banned the
manufacture and distribution of several major fluorescent lamp
types, and set minimum efficacy standards for a variety of PAR and
R incandescent lamps.
Major fluorescent lamps that are no
longer manufactured, with available alternatives, are shown in the
table below.
Major Fluorescent Lamp Types
Affected by EPACT '92
No Longer
Manufactured
|
Available
Alternatives
|
|
|
40W F40T12 (CW and WW)
|
40W and 34W triphosphor F40T12
lamps (69+ CRI)
|
|
34W halophosphor F40T12/ES CW or WW
lamps
|
|
F40T10 lamps
|
|
F32T8 lamps (requiring a compatible
ballast)
|
|
|
75W F96T12 (CW and WW)
|
75W and 60W triphosphor F96T12 (69+
CRI)
|
|
60W halophosphor F96T12 CW or
WW
|
|
F96T8 lamps (requiring a compatible
ballast)
|
|
|
110W F96T12/HO (CW and
WW)
|
110W and 95W triphosphor F96T12/HO
(69+ CRI)
|
|
95W halophosphor F96T12/HO CW or
WW
|
|
F96T8/HO lamps (requiring a
compatible ballast)
|
|
|
|
|
EPACT '92 also set minimum efficacy
standards for incandescent PAR and R lamps. These standards are
shown in the table below.
Minimum Efficacy Standards for
Incandescent PAR and R Lamps
Nominal Lamp Input Wattage
(W)
|
Minimum Average Lamp Efficacy
(Lumens per Watt)
|
|
|
40-50 W
|
10.5 LPW
|
51-66 W
|
11.0 LPW
|
67-85 W
|
12.5 LPW
|
86-115 W
|
14.0 LPW
|
116-155 W
|
14.5 LPW
|
156-205 W
|
15.0 LPW
|
|
|
|